Что скрывается за стенами самого технологичного завода Вольво? У нас есть возможность посмотреть на одно из крупнейшних производств грузовиков в России.
Экскурсия на завод Вольво в Калуге
Недавно журналистам предоствилась уникальная возможность постетить завод Вольво в Калуге. Его история началась 15 октября 2007 года — 11 лет назад — с закладки первого камня Стаффаном Юфорсом — президентом Volvo Truck Corporation, Стефано Шмелевски — президентом Renault Trucks и Анатолием Артамоновым — губернатором Калужской области. Производство расположилось на 55 гектарах Правобережного района Калуги, а инвестиции в проект превысили 100 млн. евро.
В соответствии с приказом Минпромторга РФ все грузовые автомобили Volvo калужской сборки, начиная с мая 2009 года, имеют статус отечественной техники. Уже с 2010 года начинается производство полного модельного ряда грузовиков. Сейчас завод производит 26 грузовиков в смену, а на собрку одного грузовика от начала и до конца уходит всего 16 минут. Некоторые процессы проходят на подвижной платформе, которая продвигает грузовик от станции к станции, тем самым выдерживая темп сборки.
После других российских предприятий приятно удивляет количество женщин-работниц. Здесь нет ничего удивительного: все операции по сборке и монтажу не требуют никаких тяжелых физических усилий, все легко и просто: не зря завод в Калуге — самый современый в системе заводов Volvo Group Trucks в мире. Впрочем, до полной победы над стереотипами еще далеко, и пока руководство стремится хотя бы к 17% женщин относительно мужчин.
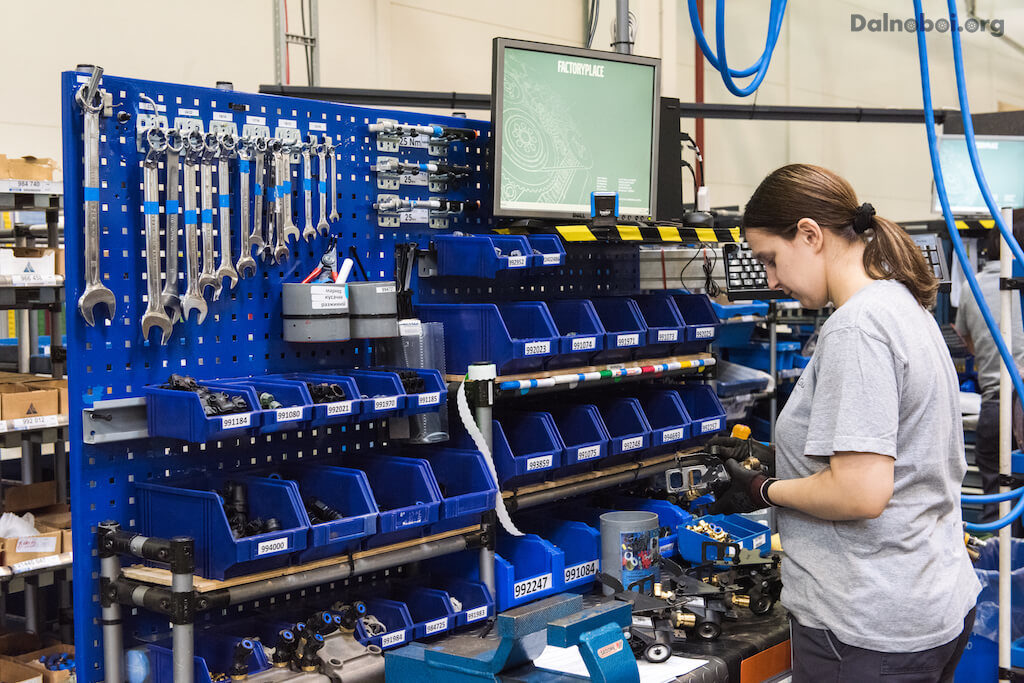
Приятно видеть порядок на рабочих местах — все подписано, все под рукой
Все заводы Вольво имеют сертификат по качеству и экологии, причем, выдается он на все заводы сразу, и если на одном будет обнаружена какая-либо проблема, сертификат будет отозван до ее устранения на всех предприятиях. Также внедрена система Volvo Production System, основанная на концепции бережливого производства, и применяется система качества Volvo, основанная на аудите готовой продукции.
Первое огромное помещение — склад. Как бы банально ни прозвучало, но сразу создается впечатление, что это — невероятных размеров Икея. Все-таки у шведов страсть к упорядочиванию вещей, видимо, в крови, и это великолепно: чистота, порядок, все аккуратно и логично. Внутри завода даже есть правила движения: есть отдельные пешеходные зоны и зоны для движения погрузчиков.
Дальше, через переход, начинаются цеха сборки. Один лишь цех Вольво занимает 15 000 кв. метров! Это 20 станций и 200 операторов. Сразу представляется муравейник с точно отлаженной работой, каждый знает свою роль и быстро и четко ее выполняет.
Около каждой рабочей станции имеется сборочная инструкция, которая включает в себя список всех действий, которые работник должен сделать, чтобы передать элемент или грузовик на следующую станцию, все используемые детали и инструменты и раскадровку процесса в картинках — ошибиться просто невозможно. Интересный момент: все детали имеют английское наименование во избежание неточностей перевода и путаницы.
Уникальное явление для российского производства — доска ямазуми для оценки эффективности производственных процессов. Ямазуми – это графический инструмент, визуально демонстрирующий составляющие источники временного цикла процесса: время на операции по сборке, время на другие действия и так далее. Визуальный контроль помогает сократить время операции за счет понимания, куда оно тратится и как его оптимизировать. Действительно удачная находка. Однако снимать ее не разрешили, поэтому поверьте на слово.
Еще одно решение, позволяющее не дать сотруднику заскучать, обучить его максимальному количеству действий и дать возможность карьерного роста в рамках производства — это матрица поливалентности. Суть ее в том, что сотрудники не работают всегда на одном и том же месте, а перемещаются от одного производственного процесса к другому в течение своей карьеры. Это позволяет понять все технологические нюансы на разных станциях, обучиться всем действиям и повысить свои профессиональные навыки, а это, в свою очередь, ведет к карьерному росту. Вообще, к обучению у Вольво особый подход: все сотрудники должны постоянно совершенствовать свои навыки, проходить обучение и курсы повышения квалификации. Для этого Вольво проводит множетсво интересных мероприятий — вспомним, например, тот же Volvo Vista для механиков. Отличный способ показать свои навыки, посоревноваться с лучшими командами из разных стран, да и что уж скрывать — получить замечательные призы и славу лучших в своем деле.
В рамках же самого завода сотрудники могут проявить свою фантазию, предложив интересную и полезную идею по оптимизации производства. Раз в квартал все предложения рассматриваются руководством, и некоторые из лучших применяются на заводе. Разумеется, любая инициатива работника — это плюсик в карьерную карму. Так что проявлять себя полезно и выгодно.
Как всегда, особое внимание Вольво уделяет безопасности: операции, связанные с важными элементами, которые могут могут обернуться риском для водителя или участников дорожного движения, проверяются трижды. Также приятно было увидеть трепетное отношение не только к технической надежности и безопасности, но и ко внешнему виду продукции: все нежные, подверженные царапинам поверхности оборачиваются чехлами при сборке!
Часть элементов российского производства, часть — шведского. Например, топливные баки и ветровые стекла на завод поставляются отечественные.
Следующий цех — цех сварки. Здесь свариваются кабины, после чего проверяются в динамической камере — информация, полученная в ходе теста, сохраняется. На кабину приходится 3000 сварных точек, а вот отверстия делаются уже под каждого конкретного клиента в зависимости от выбранной комплектации.
Сварка кузова начинается с лонжеронов и идет дальше. Для удобства есть подъемно-переворотный стол, вращающий кабину в любую сторону. Еще одна интересная система контроля качества — аудит-ареа, бокс для экстремального тестирования кабины — например, на разрыв. Позже протестированные элементы кузова вырезаются и отправляются в главный офис, в Швецию для более детального изучения. Кстати, из Швеции приходят все кузовные элементы, здесь они только свариваются и красятся.
И, наконец, последний цех — цех покраски. Контроль за безопасностью там повышен, поскольку работа проводится с красками, лаками и другими пожароопасными веществами. Снимать со вспышкой категорически запрещено! Одна из главный особенностей покраски кузова — все пластиковые элементы красятся вместе с кузовом. Благодаря этому цвет всей кабины однородный. Кузова, помимо стандартных цветов, могут окрашиваться любыми другими — для этого есть даже специальная кабина.
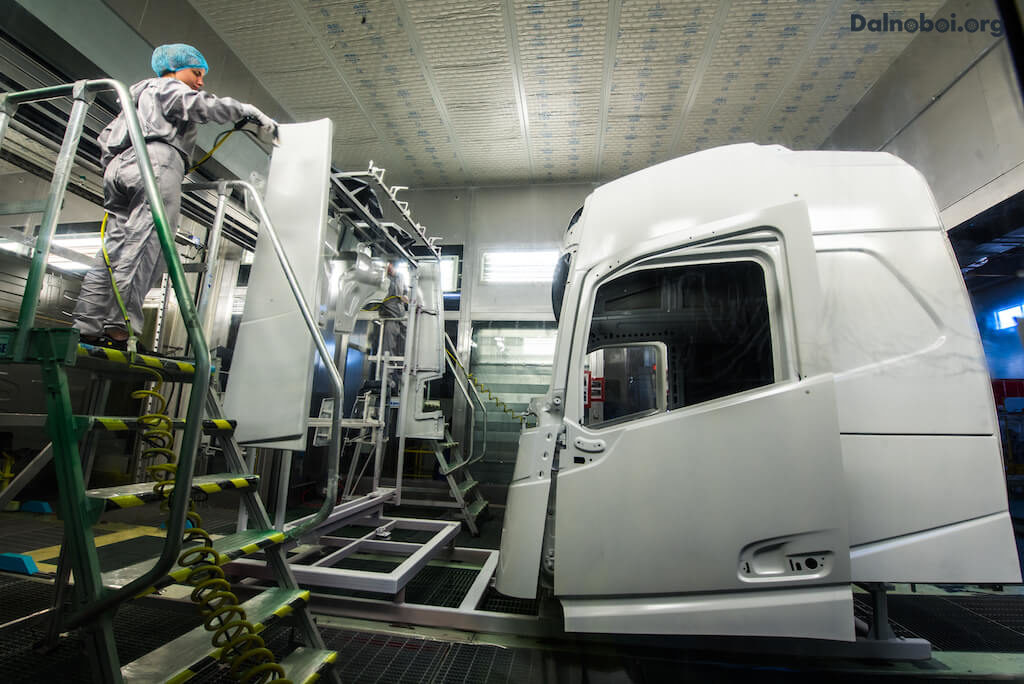
Подготовка к окраске
Немного информации: цех имеет 9 ванн, 3 из них — катафорез, также есть 8 роботов. Все стадии окраски погружные, с 4 стадиями погружения — аналогов в России больше нет. Пропускная способность цеха — 3,64 кабины в час. Лакокрасочное покрытие имеет суммарную толщину 100 микрон, из них: 20 микрон — катафорез, 9 микрон — цинк, 35 микрон — праймер, 30 микрон — сОлидный цвет.
Общее впечатление о заводе осталось самое благоприятное. Каждый процесс на виду, сотрудники — грамотные, отлично обученные специалисты, постоянно совершенствующие свои навыки на многочисленных тренингах и курсах. Технологическая начинка завода — самая, насколько это возможно, современная. Признаюсь, он разрушил мои стереотипы о том, что российское производство чем-то отличается от европейского.